In a dimly lit factory spread over 40,000 square feet near Mt. Fuji in Japan, sturdy-looking robots work round the clock with each other to create more robots. Sounds like a dystopian scene from a science fiction movie? Well, this is the automation solutions provider FANUC’s manufacturing plant. With the entire work done by robots, the factory doesn’t need lights, air-conditioners, or heating systems, significantly lowering the costs.
Robots are increasingly becoming common in factories across the globe as they help manufacturers boost productivity and profitability. According to Mordor Intelligence, the industrial robotics market was valued at $18.05 billion in 2018 and is set to reach $37.75 billion by 2024, at a CAGR of 12.15 percent.
As demand rises, major robotic automation solutions manufacturers are investing heavily to improve technology and make more efficient products for their customers. In this article, we take a look at the factors that are driving the widespread adoption of factory robots.
Machine vision and IIoT improves operations
Much research is now being done to make robots see and recognize objects. The most common tasks that factory robots undertake include assembling, inspection, quality control, and transportation. These functions require robots to capture visual information, understand and process it with data captured from other sensors.
As this technology evolves further, robots of the future would be able to integrate machine vision with machine learning to improve operations through trial and error. Technology that is classified under the umbrella-term Industrial Internet of Things (IIoT), is bringing in several new sensors that enable manufacturers to lower costs and improve efficiency through features like predictive maintenance.
Robots can now work alongside people
Cobots offer a better human-machine interaction compared to traditional robots and this results in more efficient operations. For instance, in a traditional setup, if human intervention is required at any stage of production, the entire system will have to be stopped for safety reasons. With cobots, factory employees can intervene at any point of the operations, thereby saving time and cost. Robots have been used in factories for several years now. But until recently, these were mostly crude-looking machines in enclosed spaces that were dangerous for people to go near. This has changed with the arrival of collaborative robots (cobots).
Better motors, actuators, and other components
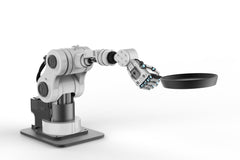
According to a report from Technavio, major manufacturers of motors and actuators for industrial robots are constantly trying to provide innovative, customized solutions. They are also boosting customer service with offers like training for customers’ employees. Along with the revolutionary changes that IIoT has brought in, there have been rapid improvements in the quality of motors, actuators, gears, gripper technology, etc. This means that robots are not just limited to large manufacturing units anymore but can also be used in industries like food and beverages where careful handling of delicate items is necessary.
Reshoring manufacturing in the US
According to a survey from the Boston Consulting Group, more and more large manufacturers in the US are considering investments to manufacture within the country, as opposed to doing it in China. Shortening the supply chain was seen as the most common reason for this, although the recent concerns on cybersecurity could provide more encouragement for this.
However, labor costs continue to remain high in the US, which means companies will have to rely on robots to avoid any losses. Costs of automation solutions continue to decrease, and this is attracting manufacturers.
Increased availability of talent
Robotic automation technology engineers weren’t common before and even the ones available were expensive. Now, realizing the potential of the sector, more and more youngsters are pursuing an education in this field. Schools and colleges are also making an effort to include this technology in their curriculum, either as a separate course or within the general education on manufacturing solutions.
Simulation software and offline programming systems that can help in testing robots are also more accessible now, making it easier for more people to enter this field.
Easier to integrate
With the progress in network technology, software development, and more computing power, setting up factory robots has become simpler and less expensive than before. Before, components like actuators and sensors had to be connected separately to robotic controllers through terminal racks, junction boxes, etc. But now they are now offered with plug-and-play technology.
Such ease of integrating the solutions in accordance with requirements is encouraging more and more end-users to opt for robots in their manufacturing units.
------------------------------------------------------------------------------------------------------------
About the Author
Prasanth Aby Thomas has written extensively on global security, automation, and smart technologies industries. He is a Senior Journalist and tech reporter and has worked with several publications in India and abroad. He completed a Masters Degree in International Journalism from the University of Bournemouth, Dorset.